Um projeto Horizon 2020 da União Europeia (UE), chamado “SMall Innovative Launcher for Europe” (também conhecido como Projeto SMILE) visa projetar um pequeno veículo lançador de satélites para lançar pequenos satélites (até 150 kg) numa órbita sincronizada com o sol, a 500 km. O Centro Aeroespacial Alemão (Deutsches Zentrum für Luft- und Raumfahrt, ou DLR) Instituto de Estruturas e Design, com sede em Stuttgart, Alemanha, é uma das quatorze organizações participantes, e é responsável pelo desenvolvimento de um injetor para motor de foguete líquido/líquido para o Lançador de projetos SMILE. O foco do Instituto num sistema de propulsão líquida deve-se ao potencial de renovação e reutilização do sistema, oferecendo, portanto, uma solução mais económica para lançadores de pequenos satélites.
“A combinação da ProX DMP 320 e do conhecimento em Design para Impressão 3D, da 3D Systems, tornaram possível testar mais opções de design em muito menos tempo.”
– Markus Kuhn e Ilja Müller, gestores de projeto de injetor, DLR
O DESAFIO
Desenvolver e produzir uma cabeça injetora altamente complexa, para um motor de foguete de combustível líquido
Tendo em vista a alta complexidade do injetor do motor de oxigénio líquido (LOX)/querosene, a DLR fez uma parceria com o Customer Innovation Center (CIC) da 3D Systems em Leuven, Bélgica, para projetar um injetor impresso em 3D que permite novas possibilidades e performance. O CIC em Leuven, da 3D Systems é um dos quatro centros mundiais dedicados a acelerar aplicações avançadas, fornecendo aos clientes acesso aos recursos necessários para desenvolver, validar e comercializar os seus produtos.
A SOLUÇÃO
Parceria para o Sucesso
Ao optar pela impressão 3D da sua cabeça injetora coaxial, a DLR procurou tirar vantagem dos vários benefícios chave do fabrico aditivo, incluindo a redução do número de peças, com um design monolítico, bem como a integração de recursos chave, como canais de arrefecimento para melhor desempenho do sistema geral de propulsão.
Markus Kuhn e Ilja Müller gerem o projeto da cabeça injetora na DLR, e dizem que selecionaram a 3D Systems como parceira devido ao histórico de sucesso da empresa de impressão 3D, na impressão 3D de metal para aplicações aeroespaciais. “Com base no sucesso das iniciativas relacionadas com o espaço, envolvendo DMP, pensámos que a 3D Systems era perfeitamente adequada para fornecer os aspetos de design para fabricação da cabeça injetora, tem em vista novas possibilidades para integração de sensores e distribuição de combustível e refrigerante”, diz Kuhn.
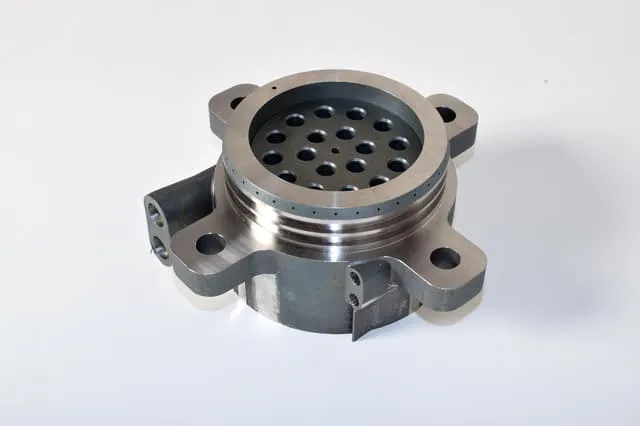
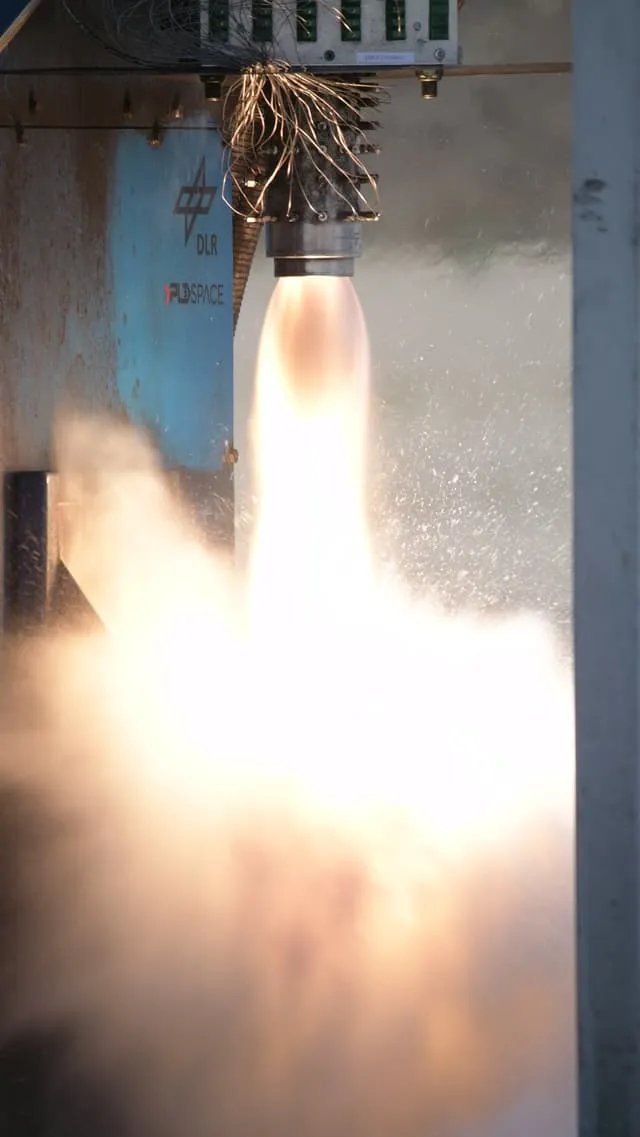
1 – Otimização do design do injetor de combustível e redução do número de peças
O injetor de um foguete é a parte pela qual o combustível e o oxidante entram na câmara de combustão. Um injetor de combustível líquido de um foguete bem-sucedido, expele esses componentes de maneira a garantir que eles se atomizem e se misturem adequadamente para produzir a combustão necessária para mover o foguete.
De acordo com Koen Huybrechts, engenheiro de projeto da 3D Systems, a cabeça do injetor de combustível líquido imaginado pela DLR, inclui vários desenvolvimentos de desempenho que foram viabilizados exclusivamente pela impressão 3D com DMP: “A necessidade de otimização de performance e arrefecimento, a complexidade do design dos canais dos sensores de pressão e temperatura, e o desejo de simplificar a montagem e a produção com processos consistentes e facilmente repetíveis apontaram para o ProX® DMP 320”, diz Huybrechts.
A Impressão 3D de metal com DMP permitiu á DLR:
- Otimizar o desempenho das peças por meio de novas oportunidades para distribuição de combustível e refrigerante;
- Fácil implementação de canais de sensor de pressão e temperatura com caminho 3D;
- Eliminar etapas intermédias de produção e montagem;
- Otimizar de forma independente, o desempenho térmico, de massa e hidráulico sem as restrições dos métodos de fabricação tradicionais;
- Evitar falhas na montagem e melhorar os aspetos de qualidade com um design monolítico;
- Reduzir as etapas de maquinação para produzir um injetor altamente integrado e multifuncional.
Ao usar a impressão 3D de metal, a DLR conseguiu alterar drasticamente a metodologia de projeto dos seus injetores coaxiais e evitar a necessidade de vários subcomponentes, o que contribuiu para reduzir significativamente o tempo e o custo de produção. Uma redução no número de peças de 30 para uma, contribuiu para uma redução final de peso de dez por cento e removeu pontos conhecidos de falha nos locais de fixação, para aliviar as medidas de controlo de qualidade relacionadas e melhorar o desempenho do sistema.
2 – Consolidando peças com impressão de precisão em metal
Os engenheiros de aplicação da 3D Systems usaram o 3DXpert para preparar o ficheiro da cabeça injetora para impressão. O 3DXpert é um software all-in-one que abrange todo o processo de fabricação aditiva de metal. A 3D Systems realizou operações de pré-impressão para facilitar a remoção do pó no pós-processamento, bem como uma verificação da printabilidade para garantir que a peça fosse construída sem complicações.
A peça final foi impressa em Leuven no CIC da 3D Systems numa impressora de metal ProX DMP 320 da 3D Systems em LaserForm® Ni718 (A), uma liga de Inconel resistente à oxidação e à corrosão. LaserForm Ni718 (A) é caracterizado por boa resistência à tração, fadiga, arrastamento e rutura a temperaturas criogénicas até 700˚C e, portanto, é ideal para aplicações a altas temperaturas.
Depois de impressa, a equipa da 3D Systems removeu o material não utilizado do interior da peça, tratou-a termicamente para aliviar a tensão e removeu-a da placa de construção usando Maquinação por descarga elétrica (EDM) com fio.
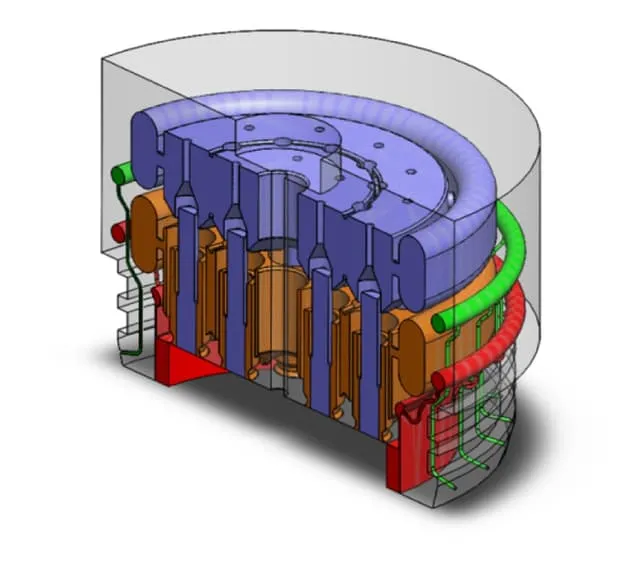
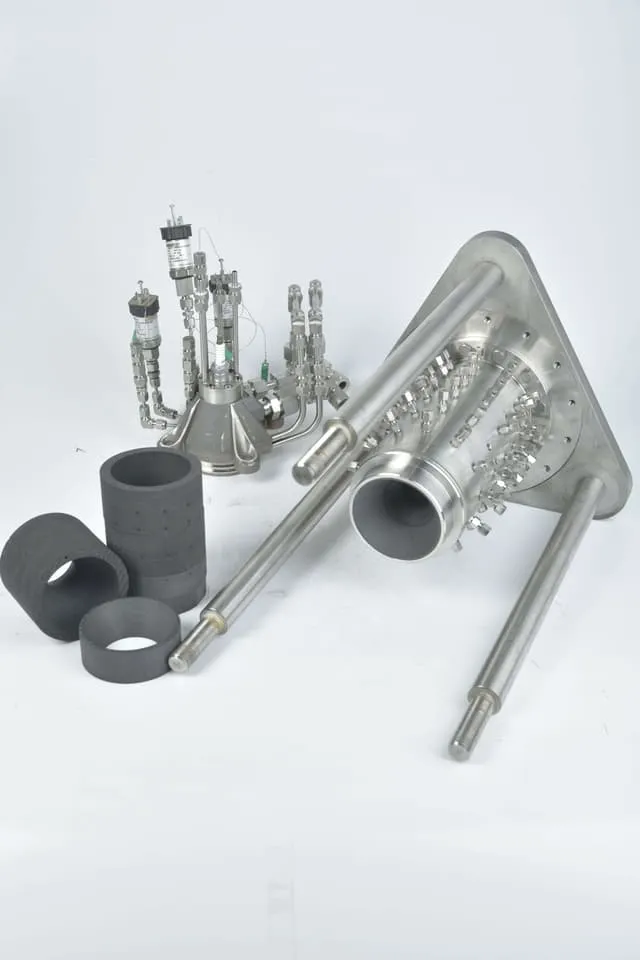
3 – Produção sem ferramentas acelera o ciclo de design
Com a expertise em manufatura aditiva e DMP da 3D Systems, a DLR foi capaz de incorporar e explorar rapidamente as mudanças de design sem a necessidade de ferramentas demoradas. Esta capacidade foi crítica para o ciclo de design do DLR, uma vez que enfrentou prazos de entrega de apenas algumas semanas para a fase um do design e teste do protótipo da cabeça injetora.
“A combinação da ProX DMP 320 e do conhecimento da 3D Systems em design para impressão 3D, possibilitou-nos testar mais opções de design em muito menos tempo”, dizem Kuhn e Müller.
A impressão 3D de metal permitiu que a DLR aplicasse técnicas de injeção coaxial com um elemento injetor de redemoinho duplo, para otimizar a mistura oxidante-combustível da cabeça injetora. Foram implementadas duas soluções de arrefecimento diferentes, cada uma usando canais finos com tamanhos mínimos de 0,2 mm e relações máximas de comprimento/diâmetro de 45. O design também integra um detalhe de colocação de filme na cabeça do injetor, permitindo que os engenheiros ajustem a taxa de fluxo de massa do filme diretamente no injetor.
4 – Maior desempenho com custos mais baixos
O DLR desbloqueou desenvolvimentos adicionais de desempenho integrando diretamente um sistema de distribuição de arrefecimento com o injetor, permitindo que os engenheiros implementassem e controlassem de forma independente a transpiração da parede e as técnicas de arrefecimento do filme. Quando aplicado dentro do injetor, forma-se um filme refrigerante na parte mais quente do lado interno da câmara de combustão, que protege a estrutura da parede de fluxos de calor elevado. Esse tipo de sistema é considerado muito mais fácil e barato de fabricar do que o arrefecimento regenerativo clássico.
Juntamente com materiais cerâmicos sofisticados, como compósitos de matriz de fibra cerâmica (CMCs), a abordagem de design e fabricação desenvolvida pelo DLR e a 3D Systems, poderia permitir que as estruturas e sistemas desenvolvidos para a cabeça injetora fossem reutilizados várias vezes e a tecnologia transferida para outras aplicações.
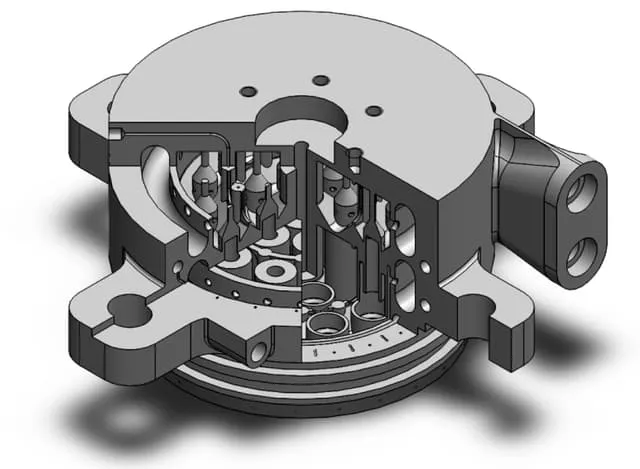
Para avaliar o novo design, o DLR realizou simulações numéricas nos fluxos internos para estimar as distribuições de combustível e as perdas de pressão associadas nas linhas de alimentação de cada propulsor. Testes subsequentes de fluxo frio mostraram uma boa correlação entre os dados medidos numericamente e experimentalmente. O teste de fogo quente para a cabeça injetora final impressa em 3D, no PLD Space na Espanha (outro parceiro do Projeto SMILE) mostrou boas eficiências de mistura e combustão em combinação com o conjunto da câmara de propulsão do foguete projetado pela DLR.
No futuro, espera-se que os novos processos de design e fabrico possibilitados pela impressão em metal, continuem a oferecer um alto grau de liberdade geométrica, menos etapas de produção para um tempo de colocação no mercado mais rápido, utilização otimizada de materiais e peças, melhorias contínuas de desempenho e melhoria na integridade estrutural para prolongar a vida útil do injetor.
“Achamos que podemos dizer com segurança que as funcionalidades integradas da cabeça injetora impresso em 3D são superiores e os tempos e custos de produção mais baixos quando comparados a peças equivalentes de última geração fabricadas por meio de métodos convencionais”, diz Müller.
OS RESULTADOS
Melhor desempenho da peça final e maior eficiência de produção
- Detalhes da peça Otimizados introduzindo melhor performance;
- Redução do número de peças em proporção 30:1 através da capacidade de consolidar o design com o fabrico aditivo;
- 10% redução de peso versus design convencional;
- Ciclos de design acelerados e custos de produção reduzidos eliminando ferramentas.
Fabrico aditivo de metal na indústria aerospacial
A impressão 3D de metal ganhou impulso como uma tecnologia-chave na aeronáutica e aeroespacial devido ao alinhamento de seus benefícios com as principais prioridades do setor, incluindo peso reduzido, economia de combustível, maior eficiência operacional, consolidação de peças, time-to-market acelerado e menos requisitos de armazenamento de peças.
Projetos recentes que comprovaram a eficácia da tecnologia DMP da 3D Systems no mercado aeroespacial incluem:
- O primeiro filtro de radiofrequência (RF) impresso em 3D testado e validado para uso em satélites de telecomunicações comerciais. O novo filtro da Airbus Defense and Space reduz o peso em 50% em relação aos designs anteriores;
- Braquetes de titânio que são 25% mais leves e apresentam uma relação rigidez/peso melhor do que os fabricados por meios tradicionais, introduzidos por meio de uma colaboração entre a Thales Alenia Space e a 3D Systems;
- Peças de motor criadas num projeto da Agência Espacial Europeia (ESA) e a 3D Systems, que economizam peso, simplificam a montagem, aceleram a fabricação e facilitam a adaptação do projeto em estágio avançado;
- Um suporte de aeronave topologicamente otimizado que reduz o peso em 70 por cento enquanto satisfaz todos os requisitos funcionais e atende ao desafio da GE Aircraft.